Yes, we do prototyping in-house. We try to keep prototyping in-house as much as possible, but it does depend on the materials needed to complete the process and the circumstances and scale of the project. We will co-ordinate your prototype – whether it is made by us or externally – as part of the project.
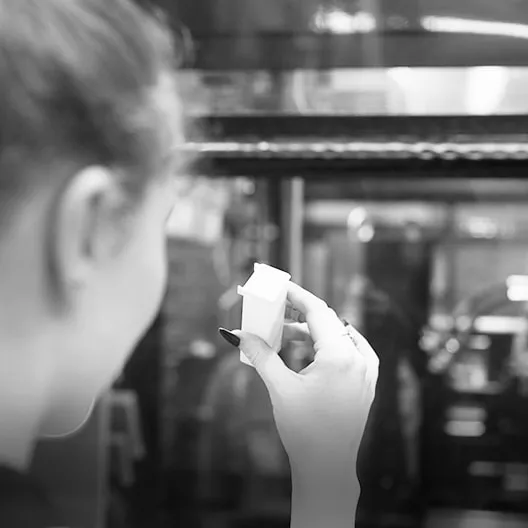
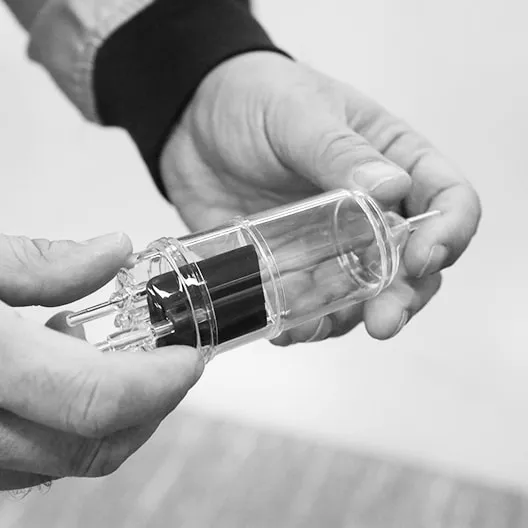
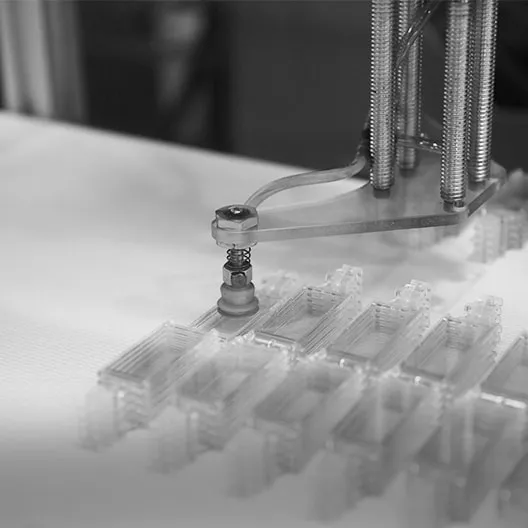
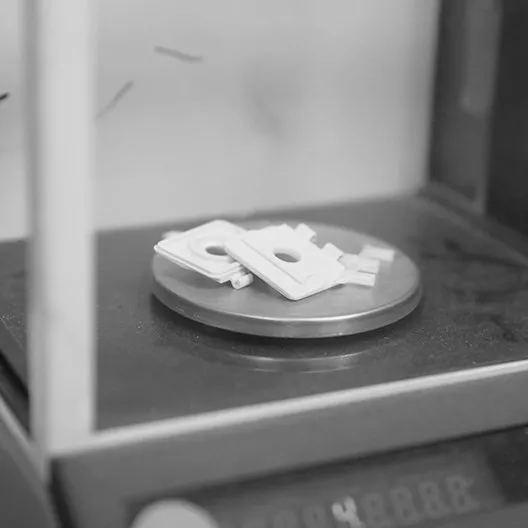
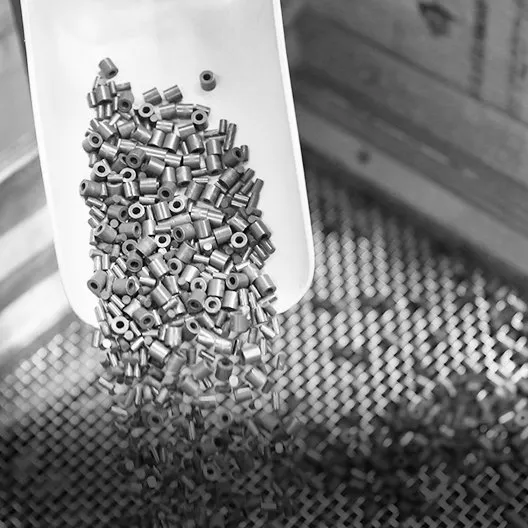